Unlocking the Potential of SolidWorks CNC Programming for Precise Manufacturing
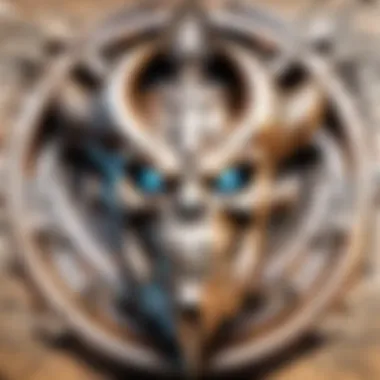
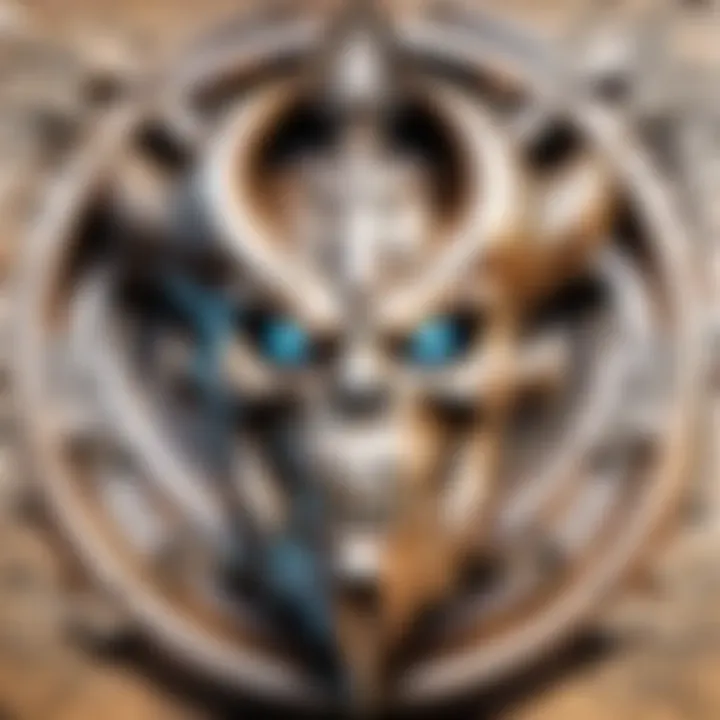
Exploring Solid
Works CNC Programming
Solid Works CNC programming opens up a world of possibilities within the realm of manufacturing.
Understanding CNC Programming Basics
Begin by unraveling the foundations of CNC programming. Delve into the intricacies of G-code and M-code, the languages that communicate with CNC machines. Discover the significance of toolpaths, feed rates, and cutting depths in programming precision.
Integrating Solid
Works with CNC Machines
Unlock the potential of Solid Works by seamlessly merging its capabilities with CNC machines. Explore how this integration streamlines machining processes, enhances accuracy, and boosts efficiency in manufacturing workflows.
Advanced Techniques and Best Practices
Elevate your CNC programming prowess with advanced techniques and industry best practices. Dive deep into topics like multi-axis machining, simulation-driven machining, and optimizing tool strategies for enhanced productivity.
Synthesizing Solid
Works CNC Programming Knowledge
As you journey through this guide, assimilate the wealth of information presented to optimize your Solid Works CNC programming skills. Harness the power of technology to revolutionize your approach to precision engineering and manufacturing.
Introduction to Solid
Works CNC Programming In the realm of manufacturing, the integration of Solid Works software with CNC machines plays a crucial role in optimizing production processes. SolidWorks CNC programming serves as the bridge between design and manufacturing, enabling precise and efficient machining operations. Understanding the fundamentals of SolidWorks CNC programming is essential for individuals involved in the fabrication industry, as it offers a powerful toolset to transform digital designs into physical components. The ability to generate toolpaths, simulate machining operations, and streamline the manufacturing workflow sets SolidWorks apart in the CNC programming domain. This section provides a comprehensive overview of the foundational principles that underpin SolidWorks CNC programming, emphasizing its significance in achieving accuracy, repeatability, and productivity in modern manufacturing environments.
Understanding CNC Machining
What is CNC Machining?
CNC machining stands as a cornerstone in modern manufacturing, revolutionizing the way components are fabricated with unparalleled precision and efficiency. At its core, CNC machining involves the utilization of computer-controlled systems to automate the machining process, enabling intricate part production with minimal human intervention. The key characteristic of CNC machining lies in its ability to execute complex operations consistently, translating digital designs into physical prototypes with exceptional accuracy. This automation-centric approach not only enhances production speed but also guarantees uniformity across multiple workpieces. While boasting exceptional advantages in scalability and precision, CNC machining also poses challenges in programming intricacies and setup requirements, aspects that warrant careful consideration in the realm of Solid Works CNC programming.
Role of CNC Machines in Manufacturing
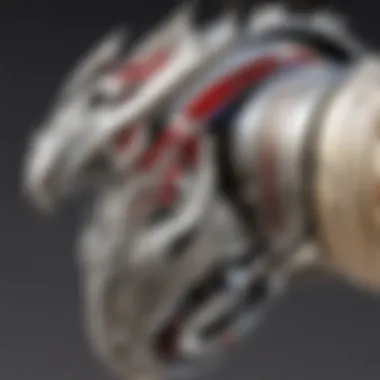
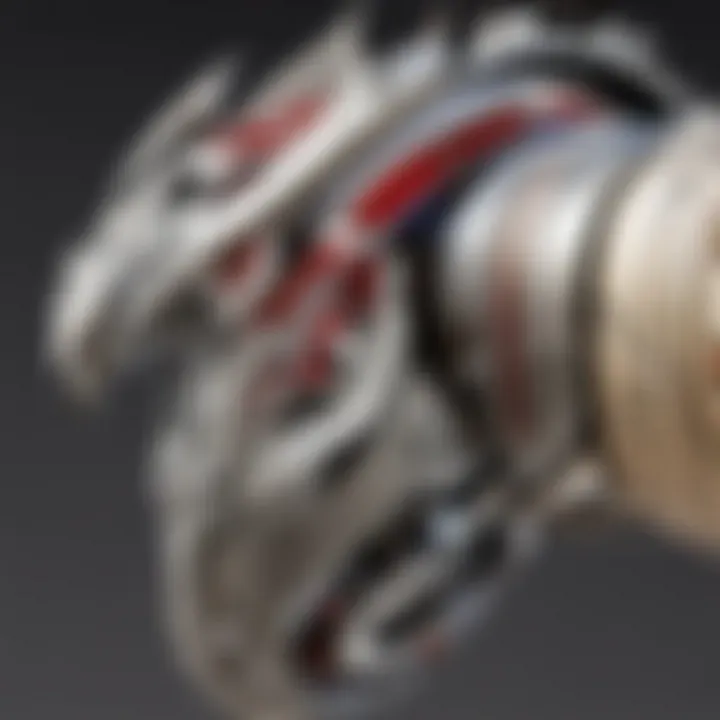
CNC machines play a pivotal role in modern manufacturing by serving as the backbone of automated production processes. Their ability to interpret design specifications and execute machining tasks with unwavering accuracy underscores their significance in the fabrication industry. The key characteristic of CNC machines is their versatility in handling a diverse range of materials, from metals to plastics, facilitating the production of complex geometries with high dimensional accuracy. This adaptability ensures that manufacturers can meet stringent quality requirements while optimizing production efficiency. However, the integration of CNC machines necessitates a deep understanding of their operational principles and constraints, emphasizing the importance of comprehensive training and skill development for operators engaging with Solid Works CNC programming.
Benefits of Solid
Works in CNC Programming
Enhanced Design Capabilities
Solid Works elevates the capabilities of CNC programming by offering advanced design functionalities that empower users to create intricate geometries with ease. Its intuitive interface and extensive feature set enable designers to conceptualize complex components efficiently, leading to shorter design cycles and accelerated time-to-market. The key characteristic of SolidWorks in enhancing design lies in its parametric modeling approach, allowing for quick design modifications and iterative improvements without disrupting the overall workflow. This flexibility translates to reduced design iterations, minimized errors, and enhanced collaboration between design and manufacturing teams.
Seamless Integration with CAM Software
The integration of Solid Works with Computer-Aided Manufacturing (CAM) software streamlines the CNC programming workflow by providing a seamless transition from design to machining. SolidWorks' compatibility with CAM platforms enables users to generate toolpaths directly from their 3D models, eliminating the need for manual intervention and data translation. This integration enhances manufacturing efficiency by automating programming tasks, optimizing toolpath generation, and simulating machining operations within a unified environment. The key characteristic of SolidWorks' integration with CAM software lies in its ability to maintain design intent throughout the manufacturing process, ensuring consistency and precision in the final machined components.
Key Concepts in Solid
Works CNC Programming
Solid Works CNC programming is a crucial aspect of modern manufacturing, revolutionizing the way components are fabricated with precision and efficiency. In this section, we delve deep into the fundamental pillars that uphold the realm of SolidWorks CNC programming, shedding light on its significance in optimizing manufacturing processes. By exploring key concepts in SolidWorks CNC programming, readers will gain valuable insights into leveraging this sophisticated technology to streamline production workflows and enhance product quality.
CAD Design for CNC
Creating 3D Models in Solid
Works:
Creating intricate and detailed 3D models in Solid Works is a cornerstone of CNC programming, laying the foundation for precise and accurate manufacturing. With its intuitive interface and advanced toolsets, SolidWorks empowers designers to bring their visions to life in a digital realm, ensuring seamless translation from virtual design to physical product. The immersive modeling environment offered by SolidWorks enables engineers to iterate rapidly, refine designs, and perform simulations to validate manufacturability, making it a preferred platform for CAD design in CNC programming.
Optimizing Designs for Manufacturing:
Optimizing designs for manufacturing is a strategic process that aims to enhance efficiency, reduce costs, and minimize production errors. Solid Works provides robust tools for design analysis, enabling engineers to identify potential manufacturing constraints early in the development phase and implement design modifications to improve manufacturability. By optimizing designs in SolidWorks, manufacturers can streamline their production processes, accelerate time-to-market, and uphold stringent quality standards, ensuring a competitive edge in the industry.
CAM Programming with Solid
Works
Toolpath Generation:
Efficient toolpath generation is fundamental to achieving optimal machining outcomes in CNC programming. Solid Works offers advanced algorithms and machining strategies that enable engineers to generate intricate toolpaths tailored to specific part geometries and machining requirements. By leveraging SolidWorks for toolpath generation, manufacturers can maximize cutting efficiency, minimize material waste, and achieve superior surface finishes, thereby enhancing overall production quality and productivity.
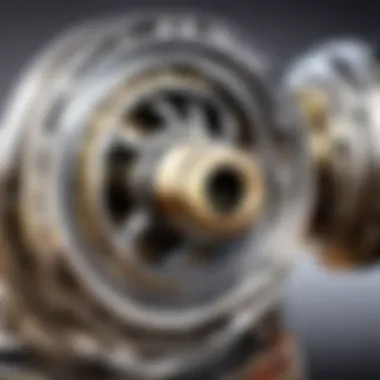
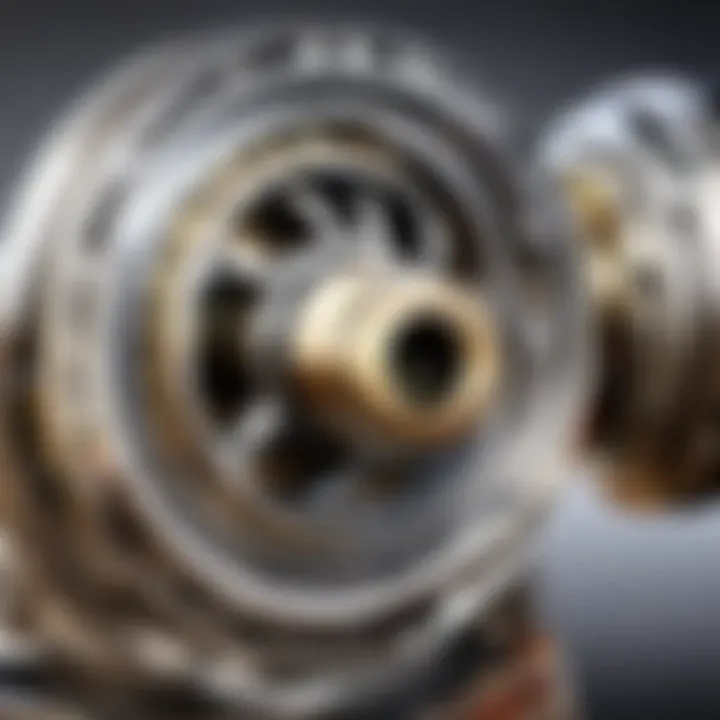
Post-Processing and Simulation:
The post-processing and simulation capabilities of Solid Works empower manufacturers to validate machining operations, analyze potential toolpath errors, and optimize cutting strategies for superior part quality. By simulating machining processes within the SolidWorks environment, engineers can identify collision risks, verify machine capabilities, and optimize production workflows before physically machining parts, reducing the likelihood of errors and ensuring cost-effective manufacturing processes.
Tooling and Machining Strategies
Selection of Cutting Tools:
The selection of cutting tools plays a pivotal role in determining machining efficiency, part quality, and production costs in CNC programming. Solid Works provides a comprehensive database of cutting tools, along with sophisticated tool selection algorithms that assist engineers in choosing the most suitable tools for specific machining operations. By intelligently selecting cutting tools in SolidWorks, manufacturers can enhance tool life, minimize machining vibrations, and achieve exceptional precision in their machining processes.
Implementing Efficient Machining Strategies:
Implementing efficient machining strategies is essential for optimizing manufacturing productivity and ensuring consistent part quality. With Solid Works, engineers can simulate and refine machining strategies, evaluate alternative toolpath options, and fine-tune cutting parameters to maximize machining efficiency. By implementing efficient machining strategies in SolidWorks, manufacturers can reduce cycle times, boost production throughput, and uphold stringent quality standards, leading to enhanced operational performance and customer satisfaction.
Advanced Techniques and Best Practices
When exploring Solid Works CNC programming, delving into advanced techniques and best practices becomes essential. This section focuses on elevating the machining process through optimized methodologies and industry standards. Understanding the importance of implementing advanced techniques can significantly impact manufacturing efficiency and precision. By leveraging best practices, operators can enhance productivity and quality outputs. Dive into this segment to uncover specific elements like toolpath optimization, custom post-processors, and more.
Optimizing Toolpaths for Efficiency
Minimizing Machining Time
In the realm of Solid Works CNC programming, minimizing machining time plays a pivotal role in streamlining production processes. By reducing the time taken for machining operations, manufacturers can enhance productivity and meet demanding deadlines with ease. The key characteristic of minimizing machining time lies in its ability to boost overall efficiency and reduce operational costs. This practice is a popular choice for organizations looking to optimize their manufacturing workflows. Despite its advantages, minimizing machining time may pose certain challenges related to tool wear and surface finish, which require meticulous planning and execution.
Reducing Tool Wear
Another critical aspect of optimizing toolpaths is reducing tool wear. By implementing strategies to minimize tool wear, manufacturers can extend the lifespan of cutting tools and maintain consistent machining quality. The key characteristic of reducing tool wear is its contribution to prolonged tool longevity and enhanced precision during machining processes. This approach is favored in Solid Works CNC programming for its ability to lower production costs and minimize tool replacement frequency. However, reducing tool wear may also lead to trade-offs in terms of cutting speeds or feed rates, requiring careful calibration and monitoring throughout the manufacturing cycle.
Implementing Custom Post-Processors
Custom post-processors play a crucial role in tailoring CNC machining workflows to specific requirements. By customizing post-processing routines, operators can optimize outputs for different CNC machines and tooling setups. Tailoring post-processing workflows offers the flexibility to fine-tune machining strategies, ensuring compatibility with varying manufacturing needs. The unique feature of custom post-processors lies in their ability to automate post-processing tasks and generate machine-specific code efficiently. While this customizability enhances production efficiency, it may introduce complexities in post-processor management and require continuous refinement to align with evolving manufacturing environments.
Automating Output Generation
Automating output generation streamlines the production cycle by automating the creation of machine-ready code from CAD designs. By automating output generation, manufacturers can reduce manual intervention, minimize errors, and accelerate the transition from design to machining. The key characteristic of automated output generation is its efficiency in transforming design specifications into executable machine instructions seamlessly. This practice is beneficial for enhancing workflow automation and reducing lead times in manufacturing processes. However, automated output generation demands robust quality control measures and thorough validation to ensure the accuracy and consistency of generated machining code.
Challenges and Solutions in Solid
Works CNC Programming
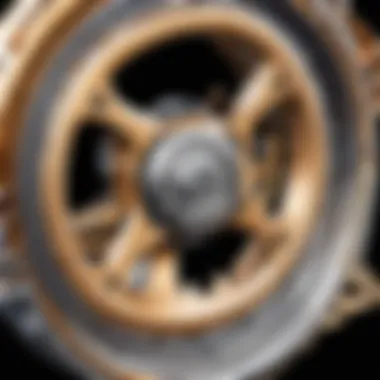
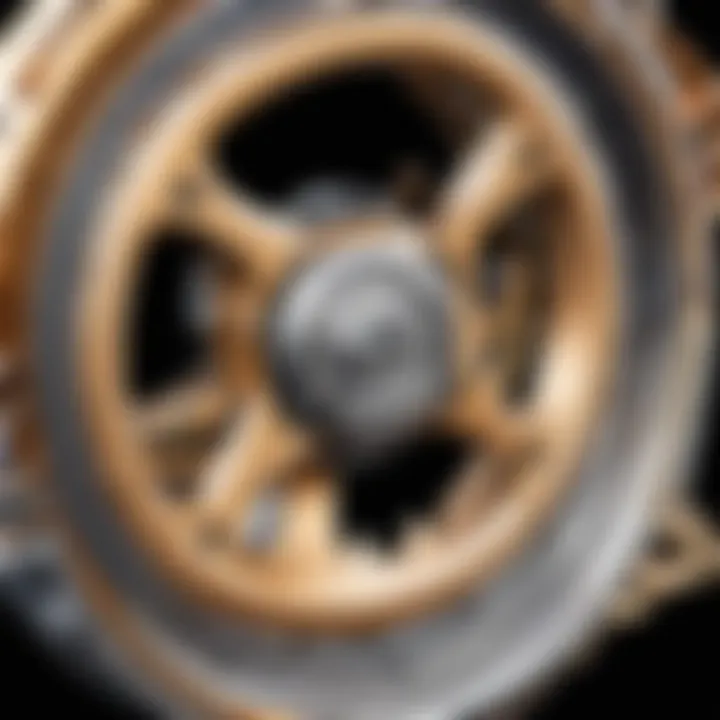
In the realm of Solid Works CNC programming, navigating through challenges and discovering effective solutions is paramount for achieving optimal manufacturing outcomes. Understanding the intricacies of CNC programming within SolidWorks software not only enhances efficiency but also elevates precision in machining processes. By delving into the challenges and solutions in SolidWorks CNC programming, individuals can fine-tune their skills and tackle complexities with a strategic approach. From addressing toolpath limitations to optimizing manufacturing precision, each aspect plays a crucial role in streamlining operations and ensuring top-notch results.
Overcoming Toolpath Limitations
Complex Geometries
When it comes to the realm of CNC programming, mastering the intricacies of complex geometries is essential for tackling varied design challenges efficiently. Complex geometries offer a sophisticated approach to design, allowing for intricate shapes and structures to be seamlessly integrated into manufacturing processes. The key characteristic of complex geometries lies in their ability to push the boundaries of traditional designs, resulting in unique and innovative products. While the advantages of complex geometries are vast, including enhanced creativity and design flexibility, there are certain limitations such as increased processing time and potential design complexity.
Multi-Axis Machining
In the realm of CNC machining, multi-axis machining stands out as a pivotal technique for achieving intricate and multidimensional designs with utmost precision. This approach enables toolpaths to move along multiple axes simultaneously, allowing for complex shapes to be machined with accuracy and efficiency. The key characteristic of multi-axis machining lies in its ability to rotate the cutting tool dynamically, accessing various angles and contours seamlessly. Embracing multi-axis machining offers a multitude of benefits, including reduced setup times and enhanced surface finishes. However, challenges such as programming complexity and toolpath optimization may arise, requiring careful consideration to maximize its advantages.
Ensuring Precision in Manufacturing
In the domain of precision manufacturing, maintaining strict tolerances and enforcing rigorous quality control measures are imperative to uphold product integrity and reliability. Tolerances and quality control parameters play a vital role in determining the accuracy and consistency of machined parts, ensuring conformity to design specifications. The key characteristic of tolerances and quality control lies in their ability to uphold strict standards throughout the manufacturing process, guaranteeing superior end products. While the advantages of stringent tolerances and quality control are evident in enhanced part accuracy and performance, challenges such as increased production costs and inspection complexities may pose hurdles.
Avoiding Collisions
When operating CNC machines, the issue of collisions poses a significant threat to both equipment and final products. By implementing collision avoidance strategies, manufacturers can mitigate risks and prevent costly damage to machinery and components. The key characteristic of avoiding collisions is the proactive approach to identifying potential clashes and rerouting toolpaths to ensure safe and uninterrupted machining operations. Embracing collision avoidance techniques offers substantial advantages, such as minimizing downtime and enhancing workplace safety. However, challenges such as intricate toolpath management and programming intricacies may require meticulous planning to effectively integrate collision avoidance into manufacturing workflows.
Future Trends and Innovations in Solid
Works CNC Programming ###
In the realm of Solid Works CNC programming, exploring future trends and innovations is crucial. As technology rapidly advances, the integration of AI in CNC programming stands out as a key focal point. The marriage of AI with CNC programming brings forth a realm of possibilities and efficiencies that were previously unattainable. AI-based toolpath optimization revolutionizes the machining process by employing algorithms to enhance toolpath planning, thereby minimizing machining time and reducing tool wear. This innovation streamlines manufacturing operations, ensuring higher precision and cost-effectiveness.
Predictive maintenance systems further contribute to the optimization of CNC programming. By analyzing machine data in real-time, these systems can predict potential failures, allowing for proactive maintenance measures to be implemented. This predictive approach minimizes downtime, increases machine reliability, and ultimately boosts productivity. Despite these benefits, challenges such as initial setup costs and data security concerns need to be addressed to fully leverage predictive maintenance systems in CNC programming.
Integration of AI in CNC Programming
AI-Based Toolpath Optimization
AI-based toolpath optimization redefines CNC programming by utilizing machine learning algorithms to self-improve toolpath efficiency. The key characteristic of this approach is its ability to adapt and optimize toolpaths based on real-time data and historical machining information. This dynamic adjustment leads to enhanced precision, reduced cycle times, and overall cost savings in manufacturing processes. However, potential disadvantages of AI-based toolpath optimization include the initial complexity of implementation and the need for knowledgeable personnel to interpret AI-generated results.
Predictive Maintenance Systems
Predictive maintenance systems play a pivotal role in CNC programming by preemptively identifying and addressing machine issues before they escalate. The standout feature of predictive maintenance is its ability to forecast maintenance requirements based on machine performance data, thereby eliminating unexpected breakdowns and enhancing operational efficiency. Despite its advantages, ensuring data accuracy and integrating predictive maintenance seamlessly into existing CNC systems pose challenges that necessitate careful consideration.
Industry 4. and Smart Manufacturing
Industry 4.0 heralds a new era of smart manufacturing, with concepts like Io T integration revolutionizing production processes. By connecting machines, devices, and systems through IoT, manufacturing facilities gain real-time visibility and control over operations. The primary benefit of IoT integration lies in its capacity to enable data-driven decision-making, leading to optimized processes and improved productivity. However, challenges related to data security and interoperability amidst diverse manufacturing infrastructures need to be addressed for successful IoT integration.
Digital Twin Technology
Digital twin technology emerges as a game-changer in smart manufacturing, offering virtual representations of physical assets and processes. The key characteristic of digital twin technology is its capability to simulate real-world conditions and performance, facilitating predictive analysis and optimization. By leveraging digital twins, manufacturers can iterate product designs, predict maintenance requirements, and enhance operational efficiency. Nonetheless, ensuring data synchronization between physical assets and their digital counterparts poses a challenge that demands innovative solutions for seamless integration.
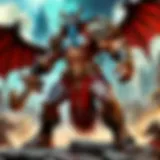
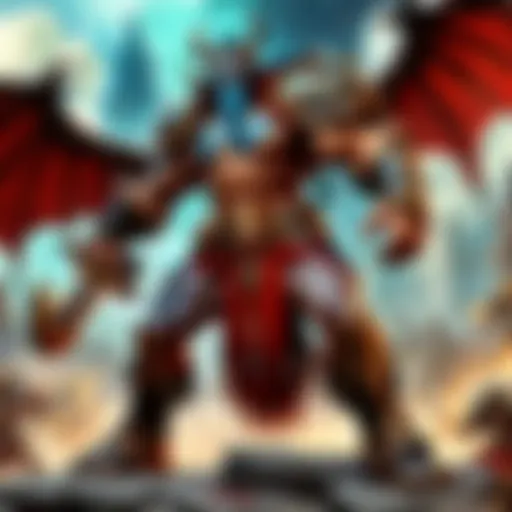